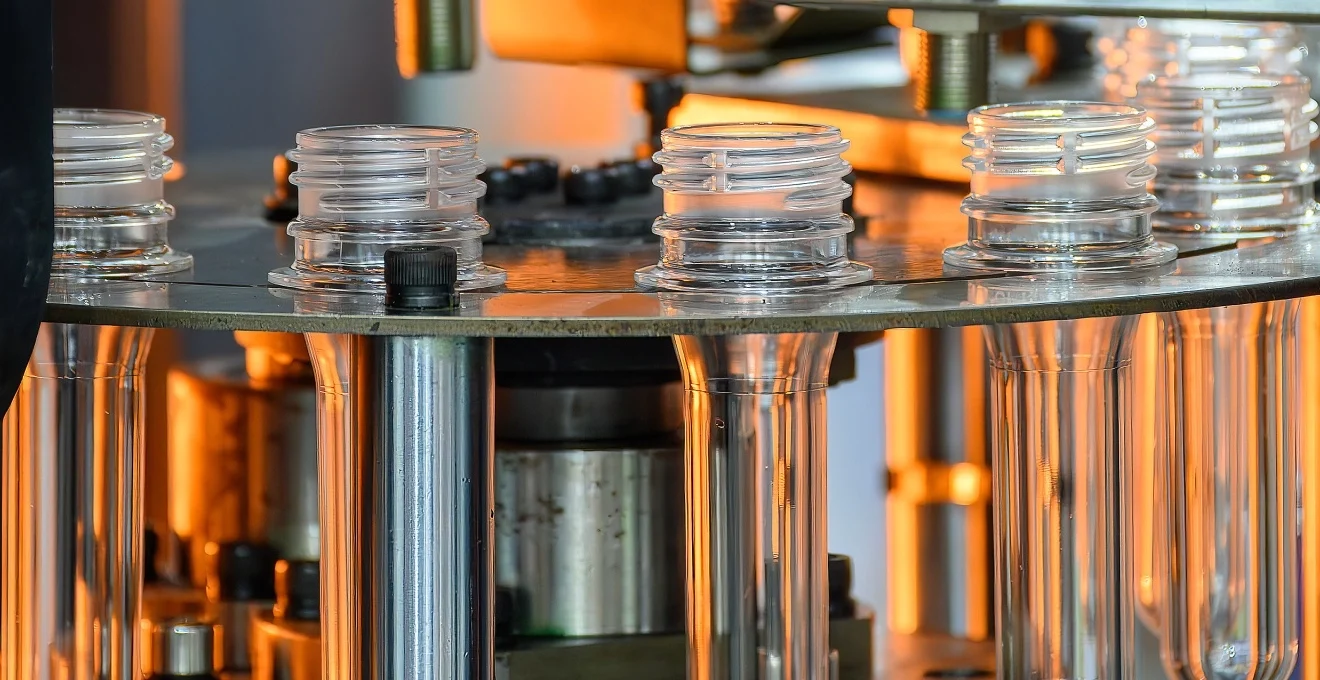
L’injection plastique s’est imposée comme une méthode de fabrication révolutionnaire, transformant radicalement les processus industriels et la conception de produits. Cette technique polyvalente permet de créer des pièces complexes avec une précision remarquable, tout en offrant une production à grande échelle économiquement viable. De l’automobile à l’électronique en passant par le secteur médical, l’injection plastique façonne littéralement notre monde moderne. Mais quels sont les principes qui sous-tendent cette technologie si influente ? Et comment continue-t-elle à évoluer face aux défis contemporains ?
Principes fondamentaux de l’injection plastique
L’injection plastique repose sur un principe simple mais ingénieux : transformer des granulés de polymère en objets finis de formes diverses. Ce processus implique la fusion du matériau plastique, son injection sous haute pression dans un moule, puis son refroidissement et sa solidification. La maîtrise de chaque étape est cruciale pour obtenir des pièces de qualité.
Le cœur du processus réside dans la presse à injecter, une machine sophistiquée qui gère l’ensemble du cycle de production. Elle comprend une unité de plastification qui fond les granulés, une unité d’injection qui propulse le plastique fondu dans le moule, et un système de fermeture qui maintient le moule fermé pendant l’injection.
La précision du contrôle de la température et de la pression tout au long du cycle est essentielle pour garantir la qualité des pièces produites. Des variations même minimes peuvent entraîner des défauts ou des inconsistances dans le produit final. C’est pourquoi les systèmes de contrôle modernes font appel à des technologies avancées pour maintenir des conditions optimales à chaque instant.
L’un des avantages majeurs de l’injection plastique est sa capacité à produire des pièces complexes en une seule opération. Des formes qui nécessiteraient autrement plusieurs étapes d’usinage ou d’assemblage peuvent être réalisées en un seul cycle d’injection. Cette caractéristique permet non seulement de réduire les coûts de production, mais aussi d’améliorer la résistance et la qualité globale des pièces produites.
Vous vous demandez peut-être comment il est possible d’obtenir une telle précision à grande échelle ? La réponse réside dans la conception minutieuse des moules et dans le contrôle précis des paramètres d’injection. Chaque moule est un chef-d’œuvre d’ingénierie, conçu pour résister à des pressions énormes tout en reproduisant fidèlement les moindres détails de la pièce à produire.
Matériaux polymères utilisés dans l’injection plastique
Le choix du matériau est crucial dans le processus d’injection plastique. Il détermine non seulement les propriétés physiques et mécaniques de la pièce finale, mais aussi les paramètres du processus de fabrication. Les polymères utilisés en injection plastique se divisent en plusieurs catégories, chacune ayant ses caractéristiques propres.
Thermoplastiques : PVC, PE, PP, PS
Les thermoplastiques constituent la catégorie la plus couramment utilisée en injection plastique. Ces matériaux ont la particularité de pouvoir être fondus et resolidifiés plusieurs fois sans altération significative de leurs propriétés. Cette caractéristique les rend particulièrement adaptés au processus d’injection et facilite le recyclage des pièces en fin de vie.
Le PVC
(polychlorure de vinyle) est apprécié pour sa résistance chimique et sa durabilité. Il est largement utilisé dans la fabrication de tuyaux, de profilés et de revêtements. Le PE
(polyéthylène) se décline en plusieurs variantes, du PEHD (haute densité) au PEBD (basse densité), offrant une gamme de propriétés allant de la rigidité à la flexibilité. Le PP
(polypropylène) est reconnu pour sa résistance à la fatigue et sa stabilité thermique, ce qui en fait un choix privilégié pour les pièces automobiles et les emballages alimentaires. Enfin, le PS
(polystyrène) est souvent utilisé pour sa transparence et sa facilité de mise en œuvre, notamment dans l’industrie de l’emballage.
Vous pouvez imaginer ces matériaux comme une palette de couleurs pour un artiste. Chaque polymère apporte ses nuances uniques, permettant aux concepteurs de créer des pièces aux propriétés spécifiques adaptées à chaque application. Par exemple, un boîtier de smartphone nécessitera un matériau résistant aux chocs et aux rayures, tandis qu’un emballage alimentaire devra être inerte et sûr pour le contact alimentaire.
Thermodurcissables : résines époxy et polyuréthanes
Contrairement aux thermoplastiques, les thermodurcissables subissent une transformation chimique irréversible lors de leur mise en forme. Une fois durcis, ces matériaux ne peuvent plus être refondus. Cette caractéristique leur confère une excellente stabilité thermique et une grande résistance mécanique.
Les résines époxy sont réputées pour leur adhérence exceptionnelle et leur résistance chimique. Elles sont couramment utilisées dans l’industrie électronique pour l’encapsulation de composants. Les polyuréthanes, quant à eux, offrent une combinaison unique de dureté et d’élasticité, ce qui les rend idéaux pour la fabrication de pièces techniques nécessitant une bonne absorption des chocs.
L’utilisation de thermodurcissables en injection plastique nécessite des équipements spécialisés et un contrôle précis du processus de réticulation. C’est un peu comme la cuisson d’un gâteau : une fois que la réaction chimique a commencé, il n’y a pas de retour en arrière possible. Cette contrainte est compensée par les propriétés uniques que ces matériaux apportent aux produits finis.
Élastomères thermoplastiques (TPE)
Les élastomères thermoplastiques (TPE) représentent une catégorie hybride, combinant les propriétés élastiques des caoutchoucs avec la facilité de mise en œuvre des thermoplastiques. Cette dualité en fait des matériaux de choix pour de nombreuses applications nécessitant à la fois souplesse et résistance.
Les TPE sont largement utilisés dans la fabrication de joints d’étanchéité, de poignées ergonomiques et de surfaces antidérapantes. Leur capacité à être injectés comme des thermoplastiques tout en conservant les propriétés élastiques des caoutchoucs ouvre de nouvelles possibilités en termes de design et de fonctionnalité.
Imaginez un matériau qui se comporte comme un caoutchouc souple mais qui peut être moulé aussi facilement qu’un plastique dur. C’est précisément ce que permettent les TPE, offrant aux concepteurs une flexibilité inégalée dans la création de produits innovants.
Bioplastiques et matériaux recyclés
Face aux préoccupations environnementales croissantes, l’industrie de l’injection plastique se tourne de plus en plus vers des solutions durables. Les bioplastiques, dérivés de ressources renouvelables comme l’amidon de maïs ou la canne à sucre, gagnent en popularité. Ces matériaux offrent des propriétés comparables aux plastiques conventionnels tout en réduisant la dépendance aux ressources fossiles.
Parallèlement, l’utilisation de matériaux recyclés connaît un essor significatif. Les technologies de recyclage avancées permettent désormais de produire des plastiques recyclés de haute qualité, adaptés à l’injection. Cette approche s’inscrit dans une logique d’économie circulaire, visant à réduire l’impact environnemental de la production plastique.
L’intégration de ces matériaux durables dans les processus d’injection plastique pose des défis techniques, notamment en termes de stabilité thermique et de reproductibilité des propriétés. Cependant, les progrès constants dans ce domaine ouvrent la voie à une industrie plus respectueuse de l’environnement. Pour en savoir plus sur les dernières innovations en matière de matériaux durables pour l’injection plastique, vous pouvez consulter les ressources spécialisées du secteur.
Machines et équipements d’injection plastique
L’évolution des machines et équipements d’injection plastique a joué un rôle crucial dans l’amélioration de la qualité, de la précision et de l’efficacité de ce processus de fabrication. Les technologies modernes permettent un contrôle sans précédent sur chaque aspect du cycle d’injection, de la fusion du polymère à l’éjection de la pièce finie.
Presses à injection hydrauliques vs électriques
Le choix entre presses hydrauliques et électriques est un débat constant dans l’industrie de l’injection plastique. Chaque technologie présente ses avantages et ses inconvénients, et le choix dépend souvent des spécificités de l’application.
Les presses hydrauliques, longtemps considérées comme la norme de l’industrie, offrent une puissance et une flexibilité inégalées. Elles sont particulièrement adaptées à la production de pièces de grande taille ou nécessitant des forces de fermeture élevées. Cependant, elles présentent des inconvénients en termes de consommation énergétique et de précision de contrôle.
Les presses électriques, en revanche, gagnent rapidement du terrain grâce à leur efficacité énergétique supérieure et à leur précision accrue. Elles permettent un contrôle plus fin des paramètres d’injection, ce qui se traduit par une meilleure répétabilité et une réduction des défauts. De plus, leur fonctionnement plus silencieux et plus propre en fait un choix privilégié pour les environnements de production sensibles.
Systèmes de contrôle numérique et automatisation
L’avènement des systèmes de contrôle numérique a révolutionné l’injection plastique. Ces technologies permettent un contrôle précis et en temps réel de tous les paramètres du processus, de la température à la pression en passant par la vitesse d’injection. L’intégration de capteurs avancés et d’algorithmes d’optimisation permet d’atteindre des niveaux de qualité et de reproductibilité inégalés.
L’automatisation joue également un rôle croissant dans l’industrie de l’injection plastique. Des robots sophistiqués prennent en charge des tâches telles que l’insertion de composants dans le moule, l’extraction des pièces finies et même certaines opérations de finition. Cette automatisation accrue permet non seulement d’améliorer la productivité, mais aussi de réduire les risques d’erreur humaine et d’assurer une qualité constante.
Vous pouvez imaginer une presse à injecter moderne comme un orchestre parfaitement synchronisé, où chaque instrument (ou paramètre) est ajusté en temps réel pour produire le résultat optimal. Cette harmonie technologique est essentielle pour répondre aux exigences toujours plus strictes de l’industrie moderne.
Moules d’injection : conception et fabrication
Les moules d’injection sont au cœur du processus de fabrication. Leur conception et leur fabrication représentent souvent l’investissement le plus important dans un projet d’injection plastique. Un moule bien conçu est crucial pour obtenir des pièces de qualité, minimiser les défauts et optimiser le cycle de production.
La conception des moules fait appel à des logiciels de CAO (Conception Assistée par Ordinateur) sophistiqués qui permettent de simuler le flux de matière et de prédire les potentiels problèmes avant même la fabrication du moule. Cette approche de conception virtuelle permet d’économiser du temps et des ressources en identifiant et en résolvant les problèmes dès les premières étapes du processus.
La fabrication des moules utilise des technologies de pointe telles que l’usinage à grande vitesse, l’électroérosion et, de plus en plus, l’impression 3D métallique. Ces techniques permettent de créer des géométries complexes avec une précision micrométrique, essentielles pour la production de pièces de haute qualité.
Périphériques : sécheurs, broyeurs, robots
Au-delà de la presse à injecter elle-même, une série d’équipements périphériques joue un rôle crucial dans l’optimisation du processus d’injection plastique. Ces dispositifs contribuent à la préparation de la matière, à la gestion des déchets et à l’automatisation des opérations annexes.
Les sécheurs sont essentiels pour éliminer l’humidité des granulés de polymère avant l’injection. Une matière insuffisamment séchée peut entraîner des défauts dans les pièces finies et des problèmes de processus. Les broyeurs, quant à eux, permettent de recycler les déchets de production en les réduisant en granulés réutilisables, contribuant ainsi à l’efficacité des ressources.
Les robots manipulateurs sont de plus en plus présents dans les cellules d’injection modernes. Ils assurent des tâches telles que l’extraction des pièces, leur inspection et leur placement dans des emballages ou sur des convoyeurs. Cette automatisation améliore non seulement la productivité mais aussi la sécurité des opérateurs en réduisant les interventions manuelles dans des zones potentiellement dangereuses.
Processus et paramètres d’injection
La maîtrise du processus d’injection plastique repose sur une compréhension approfondie de ses différentes phases et sur un contrôle précis des paramètres qui les influencent. Chaque étape du cycle joue un rôle crucial dans la qualité finale de la pièce produite.
Phases du cycle d’injection : plastification, injection, compactage
Le cycle d’injection se décompose en plusieurs phases distinctes, chacune ayant son importance dans le processus global. La plastification est la première phase où les granulés de plastique sont fondus et homogénéisés. L’injection proprement dite suit, où la matière fondue est injectée à haute pression dans le moule. Enfin, le compactage permet de compenser le retrait du plastique lors du refroidissement.
La plastification est une étape cruciale où la qualité de la matière fondue est déterminée. Une plastification inadéquate peut entraîner des défauts tels que des inclusions d’air ou des variations de densité dans la pièce finale. L’injection, quant à elle, doit être rapide et uniforme pour garantir un remplissage complet du moule avant que le plastique ne commence à se solidifier. Le compactage, souvent négligé, est essentiel pour obtenir des pièces dimensionnellement stables et sans retassures.
Contrôle de la température et de la pression
Le contrôle précis de la température et de la pression tout au long du cycle d’injection est primordial pour obtenir des pièces de qualité. La température affecte directement la viscosité du plastique fondu, tandis que la pression influence le remplissage du moule et la compaction de la matière.
Les systèmes de contrôle modernes utilisent des capteurs avancés et des algorithmes sophistiqués pour maintenir ces paramètres dans des plages optimales. Par exemple, la technique de l’injection à pression constante permet d’adapter en temps réel la pression d’injection pour compenser les variations de viscosité du plastique, assurant ainsi un remplissage uniforme du moule.
Temps de cycle et optimisation de la production
Le temps de cycle est un facteur clé dans la rentabilité de la production par injection plastique. Il englobe toutes les phases du processus, de la fermeture du moule à l’éjection de la pièce. L’optimisation du temps de cycle est un exercice d’équilibriste entre vitesse et qualité.
Des techniques telles que l’injection séquentielle ou l’utilisation de canaux chauds permettent de réduire significativement les temps de cycle. L’automatisation des opérations périphériques, comme l’extraction des pièces et leur contrôle, contribue également à l’efficacité globale du processus.
Vous pouvez imaginer le processus d’optimisation comme un chef d’orchestre ajustant chaque instrument pour obtenir la meilleure performance possible. Chaque milliseconde gagnée peut se traduire par des économies substantielles à l’échelle d’une production de masse.
Défauts d’injection et solutions correctives
Malgré tous les efforts d’optimisation, des défauts peuvent survenir dans les pièces injectées. Les problèmes courants incluent les lignes de soudure, les retassures, les bavures et les marques d’injection. Chaque défaut a ses causes spécifiques et nécessite une approche corrective adaptée.
Par exemple, les lignes de soudure, qui apparaissent lorsque deux fronts de matière se rencontrent, peuvent être atténuées en ajustant la température du moule ou en modifiant les points d’injection. Les retassures, causées par un retrait inégal de la matière, peuvent être corrigées en optimisant les paramètres de compactage.
La résolution des défauts d’injection est souvent un processus itératif qui requiert une compréhension approfondie des interactions entre les paramètres du processus et le comportement du matériau. C’est ici que l’expérience des opérateurs et l’utilisation de logiciels de simulation avancés jouent un rôle crucial.
Applications industrielles de l’injection plastique
L’injection plastique trouve des applications dans une multitude de secteurs industriels, chacun exploitant les avantages uniques de cette technologie pour répondre à des besoins spécifiques. De l’automobile à l’électronique en passant par l’emballage et le médical, l’injection plastique façonne littéralement notre monde moderne.
Industrie automobile : tableaux de bord, pare-chocs
L’industrie automobile est l’un des plus gros consommateurs de pièces injectées. Les applications vont des composants intérieurs comme les tableaux de bord et les garnitures aux éléments extérieurs comme les pare-chocs et les grilles de radiateur. L’injection plastique permet de réduire le poids des véhicules tout en offrant une grande liberté de design.
Les matériaux utilisés dans ce secteur doivent répondre à des exigences strictes en termes de résistance aux chocs, aux UV et aux variations de température. Des polymères techniques comme le polypropylène renforcé de fibres de verre ou les polyamides sont couramment utilisés pour leur combinaison de légèreté et de résistance mécanique.
L’injection plastique joue également un rôle crucial dans l’évolution vers des véhicules plus écologiques. La réduction de poids permise par l’utilisation de pièces en plastique contribue directement à l’amélioration de l’efficacité énergétique des véhicules.
Électronique grand public : boîtiers de smartphones
Le secteur de l’électronique grand public repose largement sur l’injection plastique pour la fabrication de boîtiers et de composants. Les boîtiers de smartphones, par exemple, illustrent parfaitement les capacités de cette technologie. Ils doivent être à la fois légers, résistants aux chocs et esthétiquement plaisants.
L’injection plastique permet de créer des designs complexes avec des tolérances serrées, essentielles pour l’intégration de composants électroniques miniaturisés. Des matériaux comme le polycarbonate ou les mélanges PC/ABS sont privilégiés pour leur combinaison de résistance mécanique et de qualité de surface.
La capacité de l’injection plastique à intégrer des fonctionnalités directement dans la pièce moulée, comme des clips de fixation ou des guides pour câbles, contribue à simplifier l’assemblage et à réduire les coûts de production.
Emballage alimentaire : contenants et bouchons
L’industrie de l’emballage alimentaire est un autre domaine où l’injection plastique excelle. Des bouteilles d’eau aux contenants pour plats préparés, en passant par les bouchons et les couvercles, cette technologie offre une combinaison unique de fonctionnalité, de sécurité alimentaire et d’esthétique.
Les matériaux utilisés dans ce secteur doivent être approuvés pour le contact alimentaire et offrir des propriétés barrières contre l’humidité et l’oxygène. Le polyéthylène téréphtalate (PET) et le polypropylène (PP) sont largement utilisés pour leur combinaison de clarté, de résistance et de recyclabilité.
L’injection plastique permet également de créer des systèmes de fermeture innovants, comme les bouchons à charnière ou les systèmes d’inviolabilité, qui améliorent la commodité pour le consommateur tout en garantissant la sécurité du produit.
Dispositifs médicaux : seringues, implants
Dans le domaine médical, l’injection plastique joue un rôle crucial dans la fabrication de dispositifs allant des simples seringues jetables aux implants sophistiqués. La précision et la reproductibilité offertes par cette technologie sont essentielles pour répondre aux normes strictes de l’industrie médicale.
Les matériaux utilisés dans ce secteur doivent être biocompatibles et capables de résister aux méthodes de stérilisation. Des polymères comme le PEEK (polyétheréthercétone) ou le PPSU (polyphénylsulfone) sont utilisés pour leurs propriétés mécaniques supérieures et leur résistance aux produits chimiques.
L’injection plastique permet également la production de dispositifs médicaux personnalisés, comme des guides chirurgicaux sur mesure ou des implants adaptés à l’anatomie spécifique d’un patient. Cette capacité ouvre de nouvelles perspectives dans le domaine de la médecine personnalisée.
Innovations et tendances futures
L’industrie de l’injection plastique est en constante évolution, poussée par les avancées technologiques et les demandes changeantes du marché. Les innovations récentes ouvrent de nouvelles possibilités en termes de design, de performance et de durabilité.
Injection multi-matières et surmoulage
L’injection multi-matières et le surmoulage représentent une avancée significative dans les capacités de l’injection plastique. Ces techniques permettent de combiner différents matériaux ou couleurs dans une seule pièce, offrant des possibilités de design et de fonctionnalité inédites.
Par exemple, on peut créer des pièces avec des zones rigides et souples, ou intégrer des composants métalliques directement dans une pièce plastique. Cette approche trouve des applications dans divers secteurs, de l’automobile aux produits de consommation, permettant de réduire les étapes d’assemblage et d’améliorer la qualité globale des produits.
Le surmoulage est particulièrement utile pour créer des interfaces utilisateur ergonomiques, comme des poignées d’outils avec des zones antidérapantes intégrées. Cette technique ouvre la voie à des designs plus complexes et fonctionnels, répondant aux exigences croissantes des consommateurs en termes de confort et d’esthétique.
Micro-injection pour composants miniatures
La micro-injection est une tendance émergente qui répond aux besoins de miniaturisation dans des secteurs comme l’électronique et le médical. Cette technique permet de produire des pièces extrêmement petites, parfois pesant moins d’un milligramme, avec une précision remarquable.
Les défis de la micro-injection sont nombreux, allant de la manipulation de très petites quantités de matière à la gestion de la thermique à l’échelle microscopique. Des innovations dans la conception des vis d’injection et des systèmes de contrôle permettent de surmonter ces obstacles, ouvrant la voie à la production de composants toujours plus petits et précis.
Imaginez des engrenages microscopiques pour des montres de luxe ou des dispositifs médicaux implantables ultra-miniaturisés. La micro-injection rend ces applications possibles, poussant les limites de ce qui peut être réalisé avec l’injection plastique.
Fabrication additive et impression 3D
Bien que souvent considérées comme des technologies concurrentes, la fabrication additive et l’injection plastique trouvent de plus en plus de synergies. L’impression 3D est notamment utilisée pour la fabrication rapide de prototypes et de petites séries, complémentant ainsi les capacités de l’injection plastique.
Une tendance émergente est l’utilisation de l’impression 3D pour créer des inserts ou des noyaux complexes pour les moules d’injection. Cette approche permet de réaliser des géométries qui seraient difficiles ou impossibles à usiner de manière conventionnelle, ouvrant de nouvelles possibilités en termes de design de pièces.
De plus, les avancées dans les matériaux d’impression 3D permettent désormais de produire des moules prototypes capables de supporter plusieurs centaines d’injections. Cette approche accélère considérablement le processus de développement de nouveaux produits, réduisant le temps et les coûts associés à la fabrication de moules métalliques traditionnels.
Industrie 4.0 et injection plastique connectée
L’avènement de l’Industrie 4.0 transforme profondément le secteur de l’injection plastique. L’intégration de capteurs intelligents, de l’Internet des Objets (IoT) et de l’intelligence artificielle permet une surveillance en temps réel du processus de production, ouvrant la voie à une optimisation continue et à une maintenance prédictive.
Les presses à injecter modernes sont équipées de systèmes de contrôle avancés capables de collecter et d’analyser une multitude de données en temps réel. Ces informations peuvent être utilisées pour ajuster automatiquement les paramètres de production, garantissant une qualité constante et réduisant les déchets.
La connectivité accrue permet également une meilleure traçabilité des produits, un aspect crucial dans des secteurs comme l’automobile ou le médical. Chaque pièce peut être suivie tout au long de son cycle de vie, de la production au recyclage, offrant une transparence sans précédent dans la chaîne d’approvisionnement.